Understanding the sleeve assembly: a multi-functional maintenance tool
The sleeve assembly is a multifunctional maintenance tool, composed of multiple sleeves of different specifications, suitable for the disassembly and assembly of various bolts and nuts. Whether it is home maintenance or industrial production, a set of high-quality sleeve components can greatly improve work efficiency and ensure job safety. For example, when replacing car tires, the sleeve assembly can quickly tighten or loosen the hub screws; when repairing furniture, the sleeve assembly can help you easily remove and install the screws. Through these specific examples, we can see the versatility and convenience of the sleeve assembly.
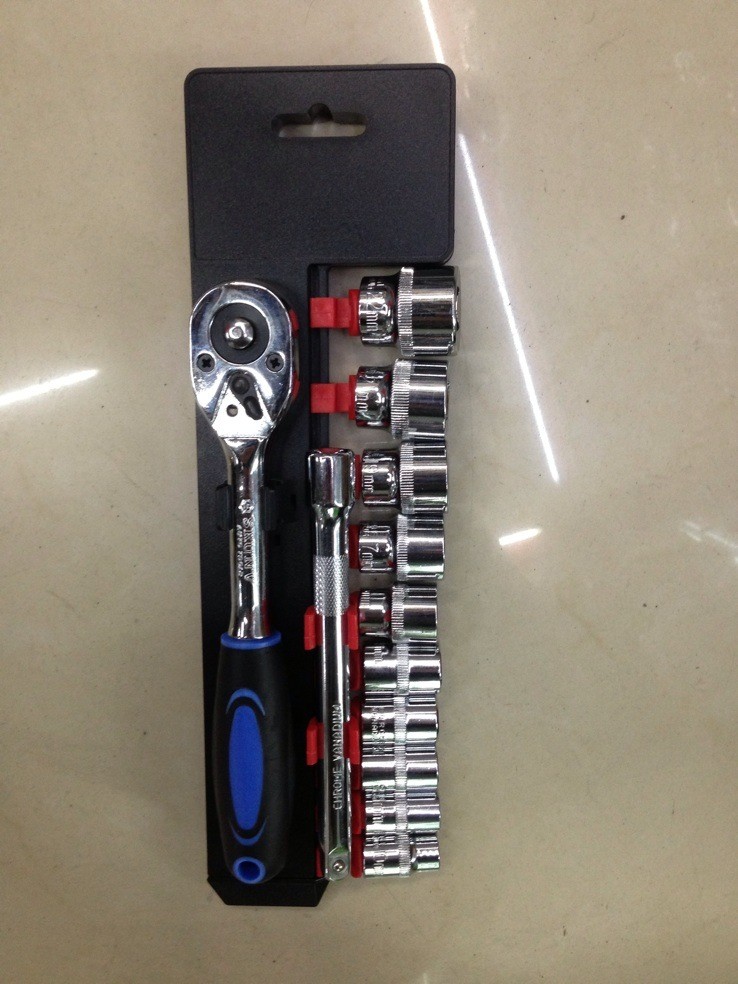
Classification and characteristics of sleeve components
Sleeve components are divided into many types according to different usage scenarios and needs, and each type has its own unique advantages. Standard sleeves are the most commonly used and are suitable for most regular maintenance tasks. The deep hole sleeve is suitable for operations that go deep into narrow spaces, such as the disassembly and assembly of bolts inside the engine. The hexagon socket is designed for special occasions and can be used flexibly in small spaces. Understanding these different types of sleeve components will help you choose the most suitable product according to your actual needs.
Quality Materials and Manufacturing Processes
The quality of the sleeve assembly directly affects its service life and performance. Common materials are chrome vanadium steel and chrome molybdenum steel, both of which have high strength and corrosion resistance. Chromium vanadium steel has good toughness and is suitable for high-load operations; while chromium molybdenum steel has higher hardness and stronger wear resistance. Advanced manufacturing processes, such as precision forging and surface treatment, can further improve the durability and reliability of the sleeve assembly. Therefore, it is very important to choose sleeve components made of high-quality materials and processes.
How to select the correct sleeve components
Choosing the right sleeve assembly requires a combination of factors. First, the working environment must be considered. Different working environments may require different types of sleeve assemblies. Secondly, tool size is also an important factor to ensure that the specifications of the selected sleeve assembly can meet your needs. In addition, the reputation and service of the brand can not be ignored. The quality of some well-known brands of sleeve components is more guaranteed, and the after-sales service is more perfect. Finally, don't forget to look at user reviews and recommend, which can help you better understand how the product actually performs.
Use and Maintenance of Sleeve Assembly
Proper use and maintenance methods can significantly extend the service life of the sleeve assembly. Before use, be sure to check whether the tool is intact and ensure that there are no cracks or other damage. During use, pay attention to moderate intensity to avoid excessive force causing deformation or damage to the tool. After use, the dirt and oil stains on the sleeve assembly should be cleaned in time, and an appropriate amount of lubricating oil should be applied to prevent rust. Properly stored in a dry and ventilated place, away from humidity and high temperature environment, can ensure that the sleeve assembly is always in the best condition.
Application of sleeve assembly in home repair
In household maintenance, the sleeve assembly is a very practical tool. For example, when you need to replace a bicycle tire, you can use the sleeve assembly to quickly tighten or loosen the wheel screws. When repairing kitchen cabinet door handles, the sleeve assembly can also come in handy to help you easily remove and install screws. Through these specific examples, you can find that the sleeve assembly is widely used in daily life, which greatly improves the maintenance efficiency and convenience.
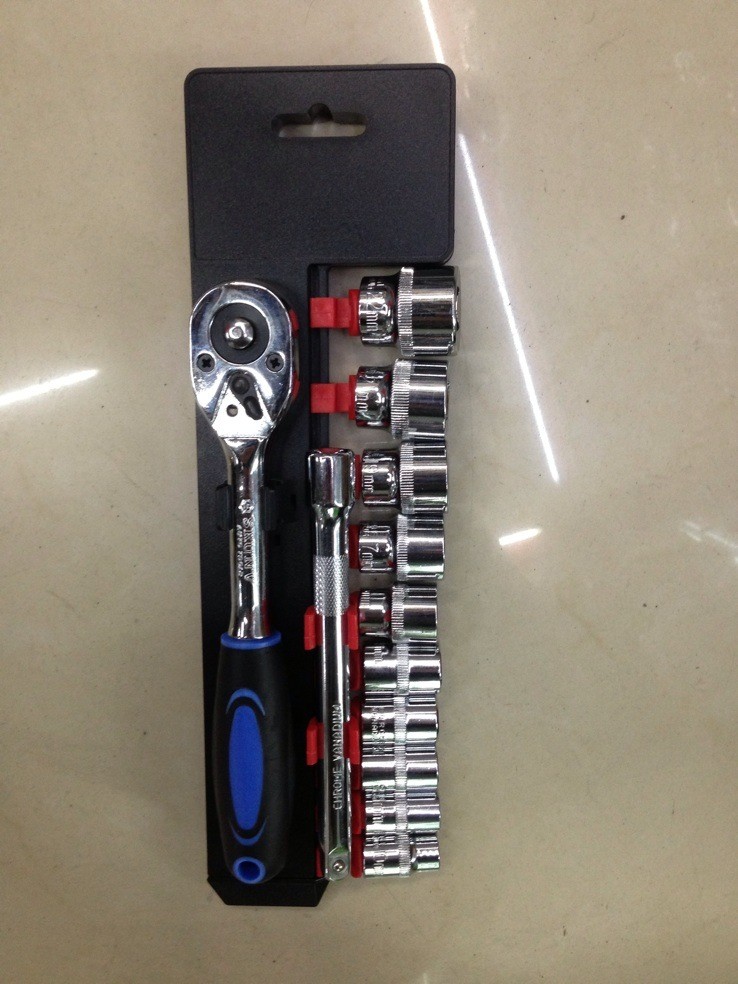
Application of Sleeve Assembly in Industrial Production
In industrial production, sleeve components play a vital role. For example, in the automobile manufacturing process, workers need to frequently disassemble and assemble various bolts and nuts. The sleeve assembly can greatly shorten the assembly time and improve production efficiency. In mechanical maintenance, sleeve components are often used for equipment maintenance and maintenance to ensure the normal operation of the equipment. Through these examples, it can be seen that the professional-grade sleeve assembly exhibits strong performance and reliability under complex working conditions.
Precautions for Safe Use of Sleeve Assembly
When using sleeve components, safety is always the primary consideration. Before operation, be sure to wear appropriate safety protective equipment, such as gloves and goggles, to prevent accidental injury. At the same time, carefully check whether the tool is intact and ensure that there are no cracks or other defects. During use, avoid excessive force to avoid danger caused by tool slippage. Regular inspection and maintenance of tools to ensure that they are always in good condition can effectively reduce safety hazards.
Future Development Trend of Sleeve Assembly
With the progress of science and technology, sleeve components are constantly innovating and developing. In the current market, lightweight design and intelligent tools have become a new trend. The lightweight design makes the sleeve assembly more portable and reduces the burden on the user. Intelligent tools through the integration of sensors and wireless communication technology, remote monitoring and data transmission, improve work efficiency and safety. Looking to the future, we look forward to more innovative technologies and design concepts applied to sleeve components,
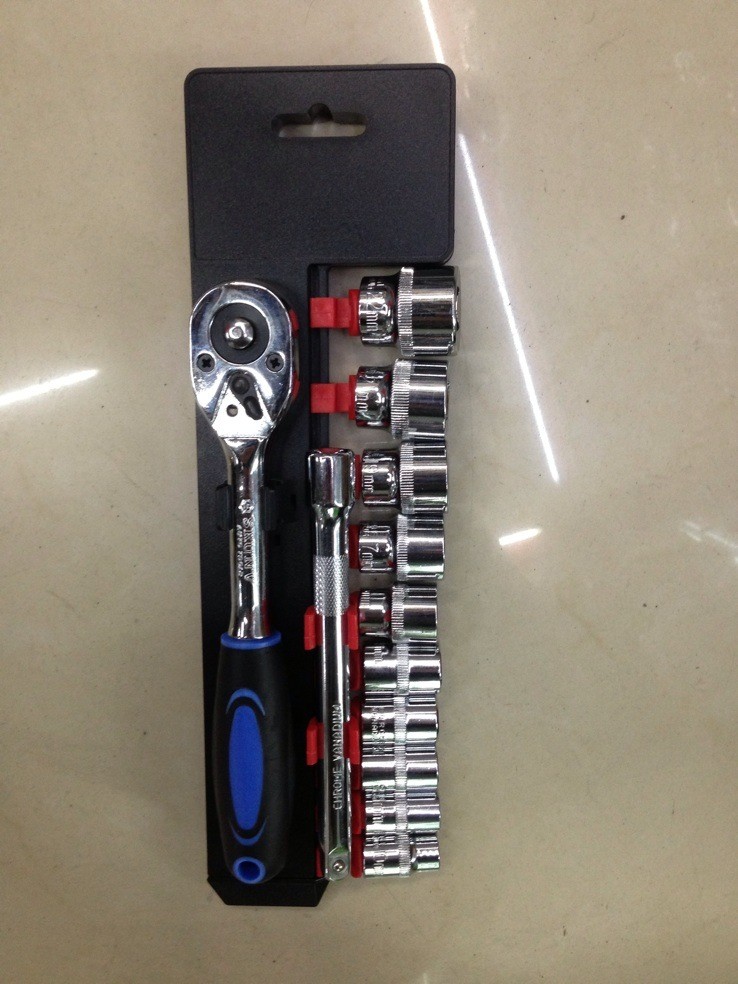