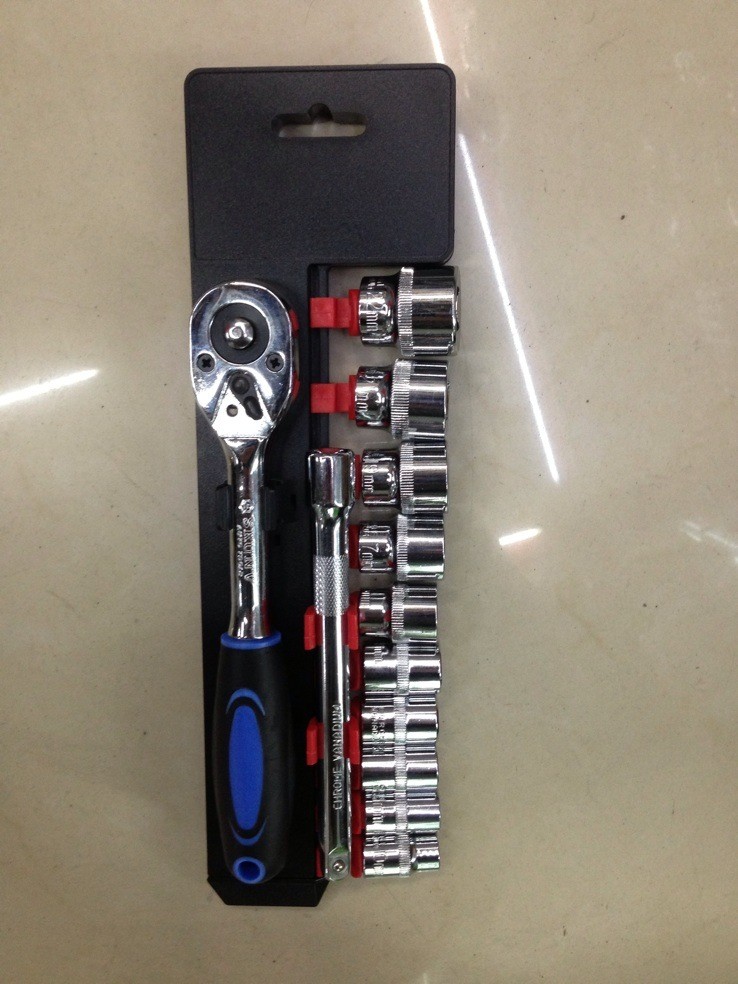
Importance of Sleeve Assembly
Whether you are a professional mechanic or a DIY enthusiast, having a high quality set of sleeve components is essential. The importance of the sleeve assembly in maintenance and assembly work cannot be ignored. First, the sleeve assembly can provide greater precision and stability, making tightening and loosening of bolts easier and more accurate. Secondly, due to its compact design, it can be operated in a small space, which is very suitable for various application scenarios such as automobile repair and mechanical equipment maintenance. Finally, the high-quality sleeve assembly is durable, which can significantly reduce the cost of tool replacement and improve work efficiency.
Basic composition of sleeve assembly
Understanding the basic composition of the sleeve assembly is essential for the correct use and maintenance of these tools. The sleeve assembly mainly includes the following parts:
Socket (Socket): This is the core part of the sleeve assembly, usually made of high carbon steel or chrome vanadium steel, with different sizes and shapes to suit nuts and bolts of different specifications.
Extension rod (Extension Bar): is used to increase the length of the sleeve so that it can be operated in a deeper position. The extension rod is also available in different lengths to cope with a variety of complex working environments.
Adapter (Swivel Joint): Connect the sleeve and the extension rod to allow a certain angle adjustment, making the operation more flexible.
Handle (Handle): Provide the part for applying torque. Common ones are ratchet wrenches, torque wrenches, etc. You can choose the appropriate handle type according to specific needs.
Type of sleeve assembly
There are many types of sleeve components to choose from on the market, each with its specific application scenario. The following are several common types, their advantages and scope of application:
Standard socket (Standard Socket): Suitable for most regular maintenance and assembly tasks, it is the most commonly used type.
Deep Socket (Deep Socket): It is specially designed for deep holes and hard-to-reach positions, especially suitable for maintenance work in the automobile engine compartment.
Hexagon socket (Hex Socket): The interior is hexagonal, which is more suitable for tightening or loosening hexagonal bolts and provides better grip.
Magnetic sleeve (Magnetic Socket): Built-in magnet can help attract bolts and prevent falling, especially suitable for high-altitude operations or operations in narrow spaces.
How to choose the right sleeve assembly
Faced with many brands and models of sleeve components, how can we choose the most suitable one? Here are some practical shopping suggestions:
Material quality: The sleeve components made of high carbon steel or chrome vanadium steel are preferred. These materials have high strength, strong wear resistance and long service life.
Specification matching: Make sure that the specifications of the selected sleeve assembly match the nuts and bolts you need to operate to avoid embarrassing situations that cannot be used.
Price factor: Although price is not the only determining factor, it is also very important to choose cost-effective products within a reasonable budget.
Brand reputation: Choose well-known brand sleeve components, usually the quality and after-sales service are more guaranteed.
Tips for using the sleeve assembly
Mastering the correct use method can greatly improve work efficiency and extend the service life of tools. Here are some common tips for using sleeve components:
Correctly install and remove bolts: Use appropriate sleeves and handles to ensure uniform force application and avoid damage caused by excessive torsion.
Deal with the stuck situation: If the bolt is stuck, you can try to spray some penetrating oil, wait for a period of time, and then try to twist it.
Reasonable selection of extension rod: According to the actual situation of the work space, choose the appropriate length of the extension rod to ensure the flexibility and safety of operation.
Care and maintenance of sleeve assembly
Good maintenance habits can keep your sleeve assembly at its best performance. Here are some simple maintenance methods:
Regular cleaning: After each use, wipe off the dirt and grease on the surface with a clean cloth to keep the tools tidy.
Check the wear: Regularly check the sleeve and handle for obvious wear or damage, and replace the damaged parts in time.
Proper lubrication: For moving parts, you can apply an appropriate amount of lubricating oil to reduce friction and extend service life.
Real Case Sharing: Application Examples of Sleeve Components
In order to give everyone a more intuitive understanding of the application of sleeve components in actual work, we share several real cases from professionals.
"As a professional mechanic, I use sleeve assemblies for car maintenance every day. I find that deep-hole sleeves are particularly convenient to operate in the engine compartment, and magnetic sleeves are also very practical, especially in confined spaces."
"I'm a DIY enthusiast and like to do small projects on my own. Standard and hex sockets are the tools I use most often. They are of very good quality and very easy to use."
FAQ
In view of the problems that users often encounter in the process of using sleeve components, we have compiled a detailed FAQ, hoping to help you solve all questions and make the use process smoother.
Q: How to judge the quality of the sleeve assembly?
A:
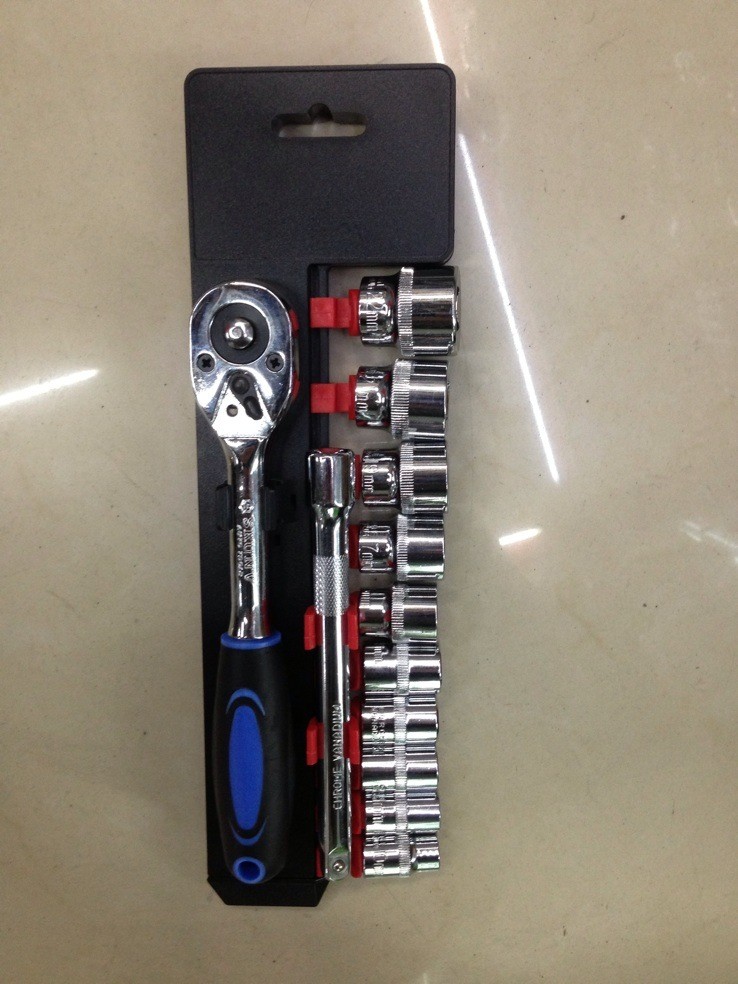