Understanding Electric Welding in Door Hinge Installation
The evolution of welding technology has tremendously impacted various industries, including the manufacturing of durable door hinges. In particular, electric welding plays a pivotal role in ensuring that these vital components meet contemporary safety and functional standards.
Key Components of Electric Welding
Basics of Electric Welding Technology
Electric welding involves the use of electrical energy to generate heat, which fuses materials together. Key principles include creating an electric arc between an electrode and the metal workpiece, producing temperatures hot enough to melt materials for fusion.
Types of Electric Welding
- MIG (Metal Inert Gas) Welding: Uses a continuous wire feed as an electrode and an inert gas shield.
- TIG (Tungsten Inert Gas) Welding: Uses a tungsten electrode; offers greater precision but requires more skill.
- Stick Welding: Utilizes consumable electrodes coated in flux; commonly used for industrial applications due to its versatility.
Essential Tools and Equipment
- Welding Machines: Necessary for generating the electric arc that causes metal fusion.
- Protective Gear: Includes helmets, gloves, and aprons to safeguard against sparks and intense light.
- Consumables: Electrodes and wires are required for different types of welds.
Importance of Strong Hinges for Heavy-Duty Doors
Heavy-duty doors such as those found in industrial settings or fire exits bear significant weight and stress. Ensuring reliable operation under these conditions is key for both function and legal compliance.
Functional Demands of Heavy-Duty and Fire Doors
These doors must handle substantial weight while maintaining smooth operation and alignment. Additionally, they often have stringent safety and regulatory requirements, especially when serving a security purpose.
Common Issues with Traditional Hinge Installation
Traditional installation methods using screws and bolts can lead to wear and tear over time, misalignment issues, and potential failures during critical moments. This reinforces the need for stronger bonding techniques like electric welding.
Advantages of Electric Welding for Hinge Installation
Electric welding addresses many problems associated with traditional attachment methods by providing enhanced strength and longevity.
Enhanced Strength and Durability
Welded joints offer superior resistance to vibrations and impacts compared to mechanical fasteners. This ensures that heavy-duty and fire-rated doors operate reliably over extended periods.
Precision and Control
Welding allows for precise placement and secure alignment, even in complex installations. The process ensures that hinges remain firmly attached, improving their operational efficiency and lifespan.
Step-by-Step Guide to Electric Welding Hinges
Preparation and Setup
Select high-quality hinges, such as the Strip hinge 201 stainless steel flag hinge, to ensure maximum durability.
Set up a safe workspace with all necessary protective gear. Choose compatible materials for the hinges and door frame to facilitate a successful weld.
Welding Process
- Tack Welding: Position and temporarily hold the hinge with small preliminary welds.
- Full Welding: Complete the weld to secure the hinge firmly to the door frame.
- Finishing Touches: Grind and smooth the welded areas to remove any rough edges and improve appearance.
Case Studies and Real-World Applications
Industrial Settings
In factories and warehouses, where durability is a priority, electric welded hinges on heavy doors ensure consistent performance despite constant use and heavy traffic.
Residential Applications
Homeowners can benefit from electric welded hinges on entrance doors and reinforced security doors, adding long-term reliability and peace of mind.
Maintenance and Inspection Post-Installation
Routine checks help identify early signs of wear and address them before they escalate into larger issues.
Regular Checks for Wear and Tear
Inspect welded joints periodically. Look for cracks, rust, or misalignments that could compromise hinge integrity.
Long-Term Maintenance Tips
- Clean and lubricate hinges regularly to prevent friction-related damage.
- Schedule periodic professional inspections to ensure optimal functionality.
Innovations and Future Trends in Welding Technology
Advances in Welding Equipment
Modern welding machines are becoming more portable and efficient. Incorporating digital tools improves accuracy and ease of use.
Emerging Techniques and Materials
Continuous advancements enhance welding methods and develop stronger, more resilient hinge materials suited for heavy-duty applications.
Expert Tips and Best Practices
Common Mistakes to Avoid
- Avoid overheating, which can cause material distortion and weakens the weld.
- Ensure comprehensive safety measures to protect yourself and your workspace.
Recommendations from Industry Professionals
Experienced welders emphasize the importance of selecting the right type of welding for specific jobs and highlight the value of proper training and certification to maintain high standards in workmanship.
Resources and Further Reading
- Recommended books and manuals on electric welding – useful for gaining theoretical and practical knowledge.
- Online tutorials and courses for hands-on learning experiences.
- Industry forums and professional organizations for networking and staying updated on the latest trends.
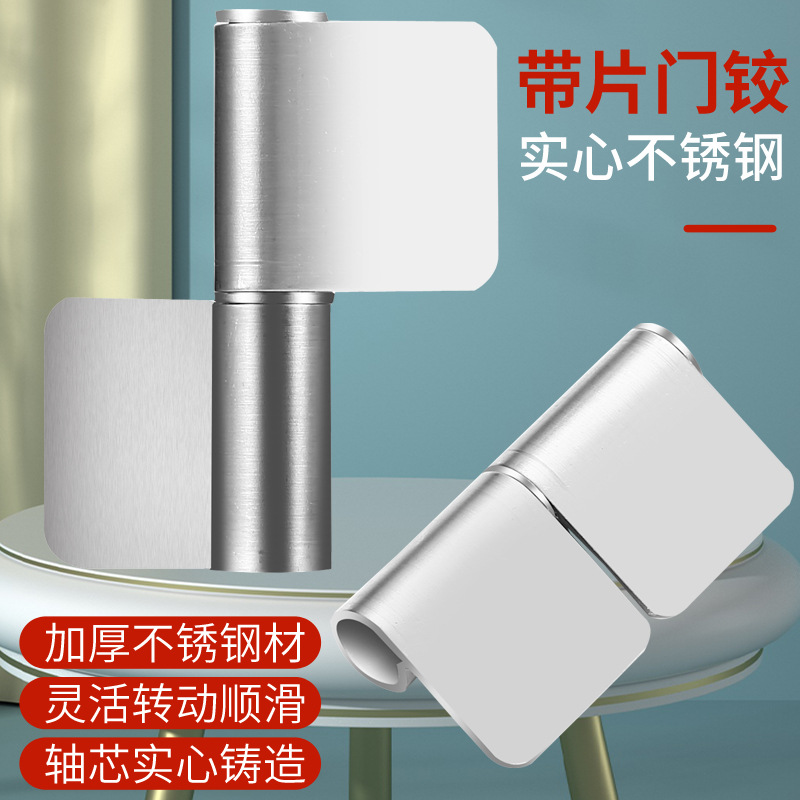