The role and importance of the sleeve assembly
In the assembly process of mechanical equipment, the sleeve assembly plays a vital role. It not only connects the various components, but also is responsible for transmitting power and bearing loads. Understanding the specific role of the sleeve assembly and its contribution to system stability can help us realize the importance of choosing the right sleeve assembly. A sleeve assembly with excellent performance can significantly improve the working efficiency of the equipment, reduce maintenance costs, and extend the service life.
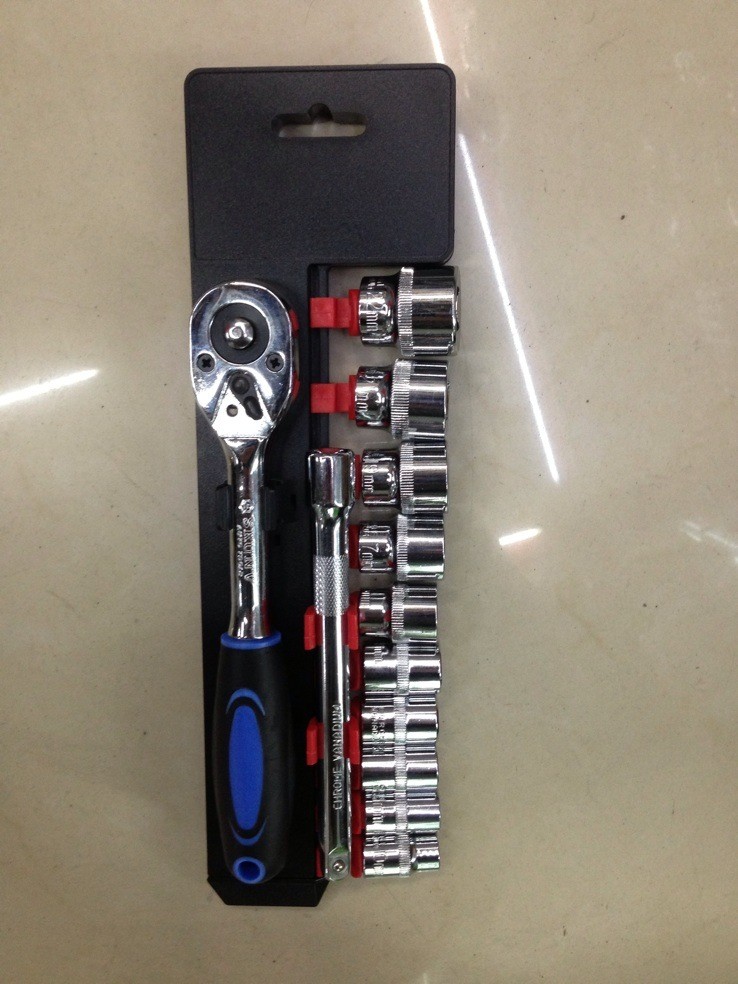
Explore the different types of sleeve components
There are many types of sleeve components on the market, each with its specific application scenarios and advantages. For example, according to the material classification, there are metal and non-metal system; according to the functional classification, there are fixed and rotary. Metallic sleeve assemblies are typically used in high load and high temperature environments due to their high strength and heat resistance. Non-metallic sleeve components are suitable for low-load and low-temperature environments because they are lighter and less prone to rust. Fixed sleeve assemblies are primarily used for static connections, while rotating sleeve assemblies are suitable for dynamic connections, allowing relative rotation between components.
How to evaluate the performance indicators of the sleeve assembly
Before choosing the right sleeve assembly, it is important to understand its key performance indicators. These indicators usually include strength, durability, wear resistance and corrosion resistance. These performance indicators can be evaluated by consulting the specifications provided by the manufacturer and the test reports issued by third-party agencies. In addition, you can consult industry professionals or refer to existing application cases to ensure that the selected components meet the high standards of the project.
Optional Guide: Selecting the Right High-Performance Sleeve Assembly for Your Project
In the face of many brands and models of sleeve components, how to quickly lock the most suitable one? This section provides several practical shopping suggestions, including determining specific application scenarios, considering cost-benefit ratios, and reviewing user reviews, to guide readers through the procurement process efficiently. The specific use environment and requirements, such as temperature range, load size, etc., help to narrow the scope of choice. At the same time, comparing the product quality and price of different suppliers, combined with the user's feedback information, can further filter out the best option.
Case Study: Examples of Successful Application of High Performance Sleeve Assemblies
Theoretical knowledge is important, but practical experience is often more convincing. In this section, we will share several real-world examples of successful applications of high-performance sleeve components, showing how they improve the overall performance of the device and solve customer-specific problems. For example, in an automobile factory, the use of high-performance rotary sleeve components greatly increased the automation of the production line and shortened the production cycle by 20%. Another example is in the field of wind power generation, the use of high-strength metal sleeve components effectively resist wear and corrosion under severe weather conditions, and ensure the safe operation of wind power facilities.
Installation and maintenance: ensure long-term stable operation
The correct installation method and regular maintenance inspection are the basis for ensuring the continuous and efficient operation of the sleeve assembly. This section details the installation steps, precautions, and common maintenance measures to help readers avoid problems caused by improper operation. Read the instructions carefully before installation to ensure that all tools are complete and in good condition. The installation should be strictly in accordance with the specified sequence and intensity of operation, to avoid excessive tightening or loosening. Regular inspection of the wear of the sleeve assembly and timely replacement of damaged parts can extend its service life. If you encounter complex problems, you should contact the professional technical support team for help.
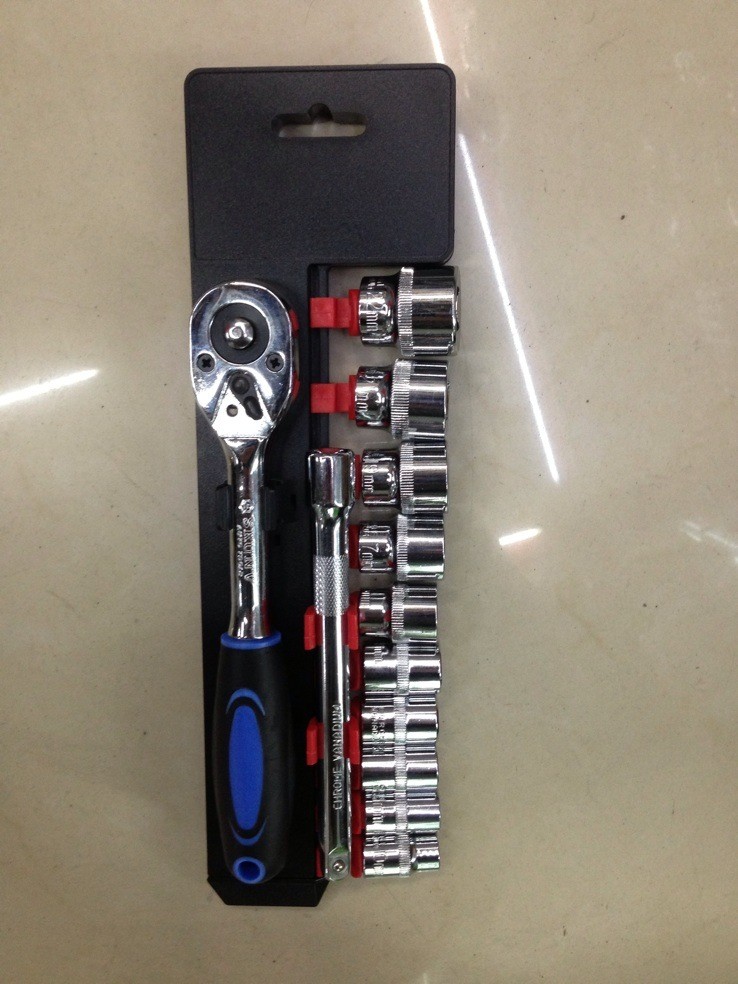