high quality Sleeve Assembly: Ideal for Tool Performance and Productivity
In daily work, a set of high-quality sleeve components often determine the convenience of operation and overall work efficiency. So what material is the key to creating the ideal sleeve? The answer is to use carefully selected alloy steels and other high-performance materials. This material not only has high strength and fatigue resistance, but also ensures long-term stability.
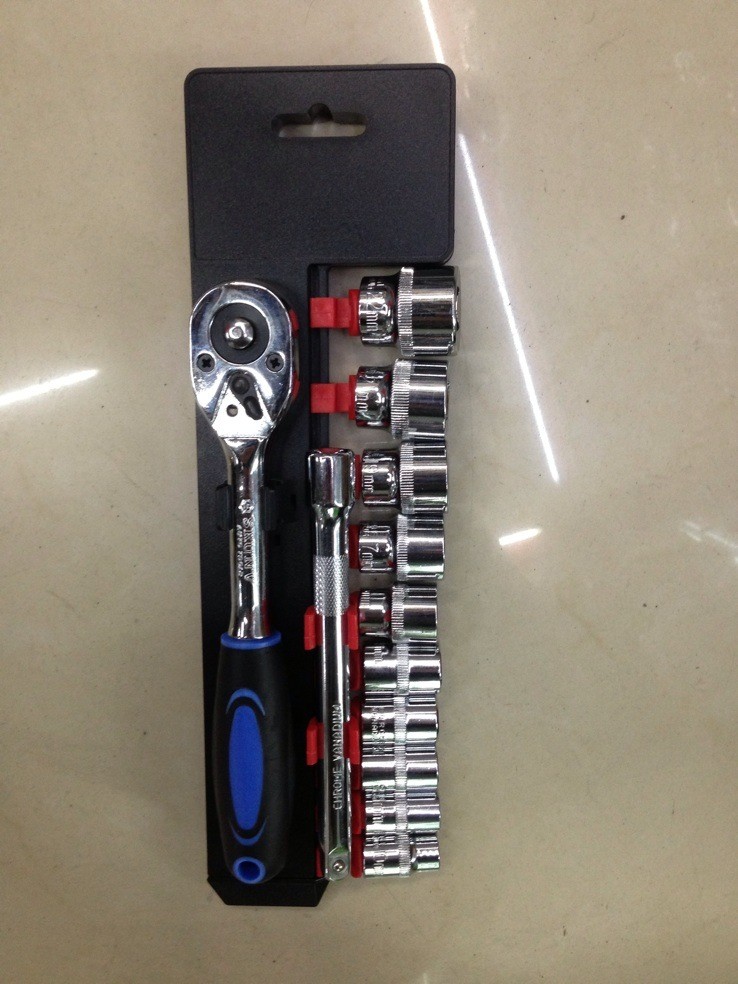
In addition to the material, the correct size match is also crucial. Each type of screw and nut has a corresponding specific specification requirement, so it is very important to choose the sleeve size suitable for your application scenario. If it is not properly selected, it may lead to the failure to complete the task smoothly or even damage the equipment parts. In order to help users find the most suitable option, we recommend carefully consulting the relevant parameter table and adjusting it according to the actual situation.
With the passage of time and technological progress, today's sleeve components have evolved from relying solely on manual production to a highly automated production line. This not only improves the accuracy of production, but also greatly shortens the delivery cycle. The modern process allows every detail to be taken care of to ensure that the ultimate quality standards of the final product are achieved.
Of course, even the best theory needs to be verified through practice. Many well-known enterprises have already felt the great changes brought about by the high-performance sleeve in the actual operation process. For example, an automobile manufacturer successfully reduced the amount of manpower input on the assembly line by nearly 30% after the introduction of a new type of sleeve, and at the same time increased the qualified rate of finished products by more than two percentage points. Similar success stories happen every day, proving that the return on this investment far exceeds expectations.
The last but not least part is how to properly maintain these valuable assets. Proper cleaning and maintenance measures can greatly delay the rate of wear and prevent corrosion. Specifically, it includes wiping the surface residue in time after each use. Regular application of anti-rust oil to protect the metal part from the external environment and other tips are very useful. As long as the implementation, I believe that every user can enjoy a longer service life.
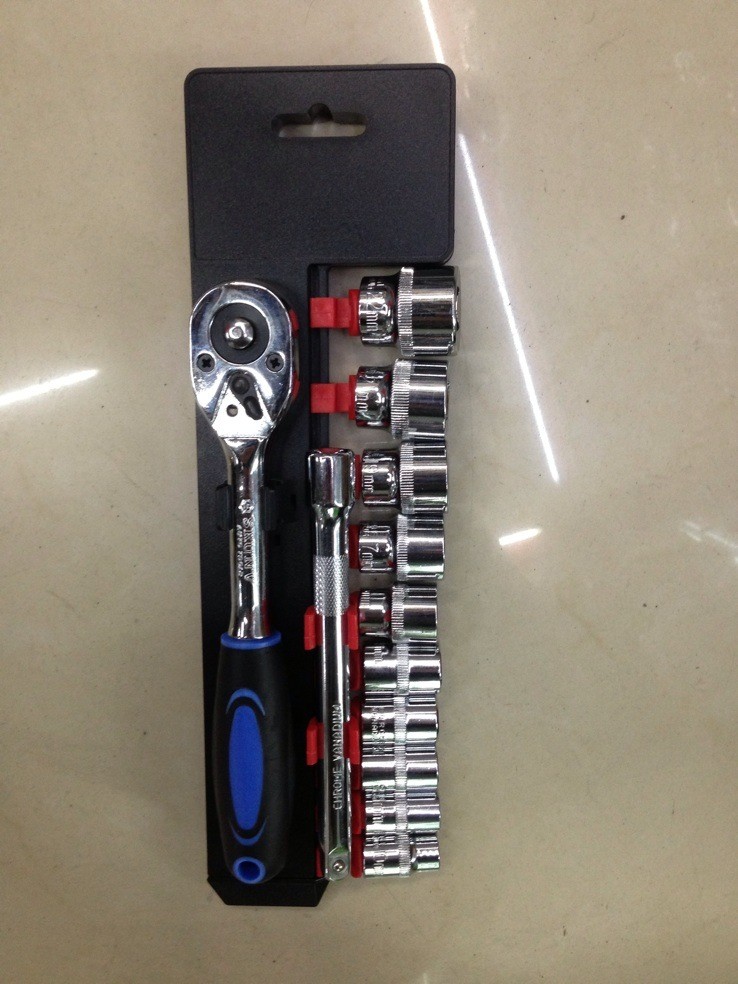