Electric welding is a vital process in the world of hardware tool manufacturing, playing a critical role in the creation of durable, high-performance tools. Electric welding is a fabrication process that joins materials, typically metals, by using high heat to melt the parts together and allowing them to cool, causing fusion. It is an invaluable technique in hardware tool manufacturing as it ensures the robustness and longevity of tools.
Understanding the basic principles of electric welding begins with understanding the physics involved. Electric welding uses electricity to generate the heat required to melt metals. The electrical energy is converted into heat energy, which then melts the metal at the welding point. There are several types of electric welding techniques such as arc welding, resistance welding, and electron beam welding. Each technique has its own set of pros and cons. For instance, arc welding is versatile and affordable while resistance welding is fast and efficient, but each may not be suitable for certain types of metals or specific manufacturing requirements.
The process of electric welding in hardware tool manufacturing can be broken down into three stages: the preparation stage, the welding stage, and the cleanup stage. In the preparation stage, the materials to be welded are cleaned and any protective coatings are removed. The welding stage involves the actual welding process where the parts are joined together. The cleanup stage includes removing any welding slag and checking the quality of the weld.
Quality assurance is crucial in electric welding. Standard protocols are in place to ensure that the welding process results in robust and durable tools. These protocols may involve visual inspections, destructive testing, and non-destructive testing. Quality assurance plays a significant role in ensuring the robustness and longevity of tools, contributing to the overall value and effectiveness of the final product.
Electric welding plays a significant role in the production of various hardware tools. For instance, in the production of screwdrivers, electric welding is used to join the handle and the steel rod. In the case of pliers, the two halves are welded together to create a durable and functional tool. These real-world examples highlight the importance of electric welding in hardware tool manufacturing.
While electric welding is a powerful tool in manufacturing, it also requires careful safety precautions. During the welding process, precautions must be taken to protect against heat, sparks, and fumes. Safety gear such as welding helmets, gloves, and respirators are essential. Post-welding cleanup also needs to be handled safely to prevent injuries from hot materials or sharp edges.
Looking towards the future, technological advancements continue to shape the landscape of electric welding in hardware tool manufacturing. Innovations in welding technology are leading to more efficient and precise welding techniques. These advancements will undoubtedly have a significant impact on the hardware tool manufacturing industry by improving productivity, product quality, and worker safety.
One such example of a product that benefits from the electric welding process is the 201 Stainless Steel Strip Hinge. This innovative, thickened, non-holed electric welding strip hinge is designed for removable fire doors. The electric welding process ensures the robustness and durability of the hinge, making it a reliable and long-lasting hardware solution.
Electric welding, as a key process in hardware tool manufacturing, is integral in the creation of durable and high-quality tools. As technology continues to advance, the possibilities for electric welding in hardware tool manufacturing are bound to expand, promising an exciting future for the industry.
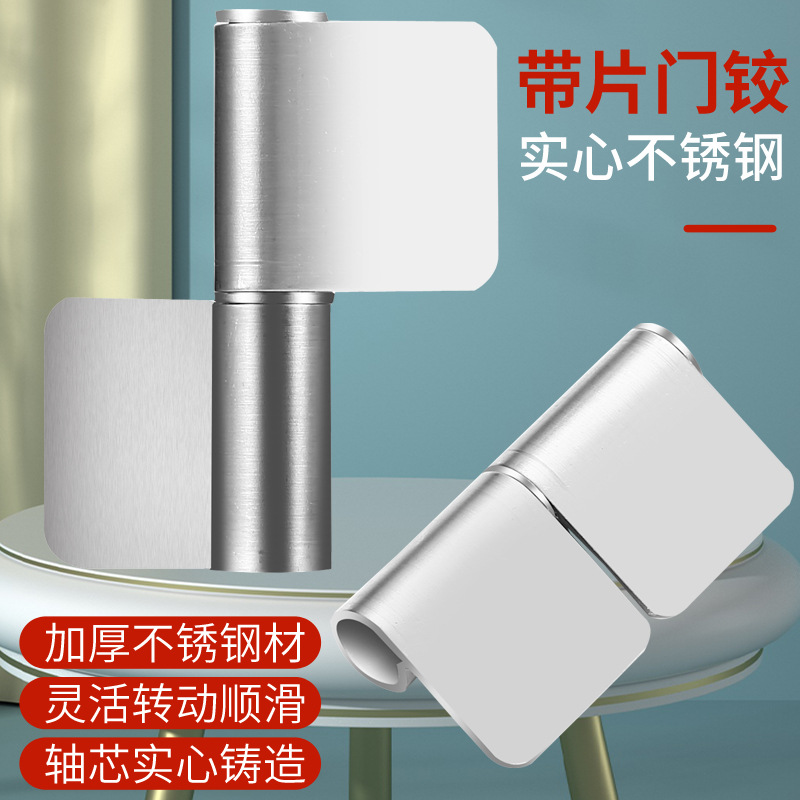